Compressed air is probably the most widespread energy carrier in industry and trade. The uses of this gas oder carrier are numerous and offer significant advantages: simplicity of use, high available power, absence of electrical risks, ease of network extension.
1. Compressed air production requirements and costs
The production of each usable working unit of compressed air requires the use of 10 to 20 units of electrical energy. This high cost is mainly due to two factors:
a) Compressed air pressure and quality requirements
There is no single solution for a carpentry workshop or body shop, a sandblasting station, a tyre inflator or a hospital. Production and air treatment technology must therefore be designed with care: too stringent requirements increase production costs, while substandard quality can lead to malfunctions or even production stoppages at consumer level.
The pressure setting of the compressed air production unit depends on:
- End-use requirements;
- Pressure losses existing between the production source and the points of use.
Air quality is defined by standard ISO 8753-1. Quality classes apply to solid particles, residual moisture (dew point) and total oil content.
b) Production machinery technology
Several types of compressors exist on the market and meet specific needs. The most common types are:
- Rotary screw compressors; reliable, easy to maintain and offer a large range of flows.
- Piston compressors; simple to operate and available in a wide variety of pressure ranges. However, they operate less efficiently than screw compressors and are limited to low flow rates.
- Multi-stage machines; more efficient and generally preferable to single-stage machines. The additional purchase cost is quickly offset by better energy performance.
Specific consumption (in kWh/m3) is the indicator used to characterise the energy performance of a compressor installation. This varies according to the final pressure, the type of compressor used, its age and its manufacturing quality. Knowing this value is important in order to be able to select the best equipment.
Real costs of producing compressed air
A "life cycle cost analysis" assessment shows that the most important cost item is the energy consumed.
In conclusion: often it is more advantageous to invest in efficient, energy-saving equipment, as the price difference can be more than compensated by the energy savings.
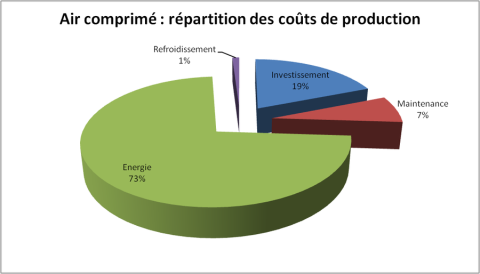
Compressed air: breakdown of production costs
- 73% energy
- 19% investment
- 7% maintenance
- 1% cooling
2. In practice: potential improvements
Adjusting the pressure as accurately as possible
Keep the pressure as low as possible without compromising working conditions: any excess pressure is a waste.
Potential savings: a pressure reduction of 0.5 bar on a network at 7 bars results in an energy gain of approximately 4%.
Reduction of needs by replacement of tools
Tools powered by electricity are much more energy efficient than those powered by compressed air.
Potential savings: up to 40% in energy consumption.
Waste reduction and user awareness
- Discourage energy-intensive operations, such as: blowing smth out?, floor cleaning or cooling machines or parts using compressed air.
- Prioritise the purchase of energy-efficient equipment;
- Maintain hoses and accessories in good condition;
- Carry out leak elimination campaigns.
Ageing networks have many leaks that need to be detected and repaired as soon as possible. Unused branches should be removed for the same reason. Network elements should be checked in operation using a portable ultrasonic detector that makes it possible to detect and quantify the order of magnitude of the leaks.
Potential savings: up to 20% in energy consumption1. A 1 mm Ø hole at 7 bars costs up to €800 per year!
Preventive maintenance
Proper maintenance of compressors ensures optimum performance and good reliability.
Potential savings: regular replacement of filters saves about 2% in energy consumption1.
Condensate trap management
Where possible, use electronic traps: these only activate when necessary and therefore reduce air loss.
Modern installations are more efficient and easier to maintain in working order.
Improving compressor adjustment
The best adjustment of the set pressure may be achieved by automating the start-up sequence of the compressors to give priority to the most efficient machine.
Potential savings: up to 12% in energy consumption.
Use of variable speed drives
It is recommended to have a variable speed compressor for each installation. This type of compressor automatically adapts to variations in flow rate and avoids periods of idle operation and untimely start-ups.
Potential savings: up to 15% in energy consumption.
Compressor replacement
Depending on requirements or the need to replace outdated equipment, it may be necessary to replace an old compressor with a modern, more reliable and more efficient model. Oversized equipment should be avoided, as it will often operate in a non-optimal way (frequent start-ups) or at no load (no-load operation before shutdown).
Heat recovery
A compressor produces large amounts of heat: up to 96% of the electrical energy introduced is dissipated as heat. This waste heat can be recovered to satisfy other low temperature needs:
- preparation of domestic hot water
- building heating
- pre-heating or drying of materials
Potential savings: 20 to 80% of the energy consumed can be recovered1.
Other potential improvements
- Install the air intakes in a clean, cool and ventilated area
- Provide effective cooling to limit the compressor operating temperature
- Improve air treatment
- Have a rational and scalable distribution network